December 2020
Inside the Newsletter:
2021 Intern Project | Preventing Pollution in Metal Fab | Energy Efficiency in Metal Fab | Optimize Water Use in Metal Fab | Funding Opportunities
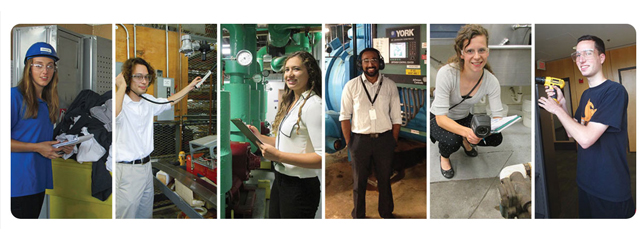
Now is the Time! Call MnTAP to Plan Your Project for 2021!
Are you ready to optimize your process, minimize waste and decrease operating costs? Could you use some help with water and energy conservation in 2021? Apply online or call NOW to schedule your appointment with a MnTAP specialist to discuss technical assistance and intern project proposals for 2021.
MnTAP anticipates supporting up to 15 projects that could focus on water conservation, energy efficiency, paint efficiency, solid waste, and pollution prevention. Check out Solutions 2020 to get an idea of what your MnTAP Intern could do in your operation. For more information about the MnTAP Intern Program or the application process, please visit the Intern Program section of our website, For Business.
Applications are currently being accepted and will be reviewed upon receipt. Companies will be contacted by MnTAP technical staff within two weeks for additional project development and scoping. Although applications are accepted until February 2021, apply today for the best chance of being selected.
This past summer was the first experience for Sappi to partner with MnTAP’s intern program. The performance of our intern was beyond expectations and has changed our belief regarding summer interns. The work will help Sappi reduce energy use and cost – immediately and long term. We are already thinking about a project for our next MnTAP intern.
~ Robert Schilling, Environmental Manager, Sappi, Cloquet, MN
If you would like to discuss a potential intern project, contact:
Matt Domski – Intern Program Manager
612-624-5119
mdomski@umn.edu
Preventing Pollution in Metal Fabrication
The pretreatment process can result in significant amounts of waste including solvents and other chemicals. By implementing pollution prevention options, your facility can reduce the amount of waste generated and save money. Additionally, some of the solvents used in the pretreatment process can be hazardous; reducing their use can decrease overall site risk.
Precision cleaning is an important aspect of metal working. The pretreatment process can result in many types of waste: solvents, chemicals, hazardous waste and wastewater loading. Understanding the cleaning criteria, type of contaminant and surface geometry are a good first step. Changing from solvent based cleaning to aqueous cleaning can reduce volatile organic compounds (VOCs) and reduce permitting and hazardous waste disposal costs. Our recent work in TCE Alternatives can provide guidance on how to not make the best change for your business.
Machining coolants are an important component of metal working operations. Coolants affect the overall performance of machining operations, and should be suitable for the type of metal and machining operation to produce the desired finish quality. Monitoring the pH and concentration of the coolant is necessary to optimize performance and prevent problems. Check out MnTAP’s Fact Sheet for Coolant Maintenance for Machining Operations for more information.
Daniel Chang – Associate Engineer
612-624-0808
dwchang@umn.edu
Energy Efficiency in Metal Fabrication
Energy use is relatively high in a variety of machining and metal fabrication facilities and a range of opportunities in a variety of process areas exist for energy efficiency improvements. For example, thermal savings can be found by making sure your burners are operating as efficiently as possible and your burner controls are working properly. Electrical savings can be found in a variety of projects that use powered equipment effectively, such as compressed air auditing; welding control; motor, fan, and pump optimization; and lighting improvements. There are a number of cross-sector technology opportunities that can result in energy conservation in metal fabrication facilities.
Process Motors, Pumps, and Fans
Combined motor, pump, and fan components are sources of 37-47% electrical utility consumption in metal fabrication facilities. Several resources exist that discuss the evaluation and proper sizing of pumps, fans, and electric motors. Programs to replace older motors could result in energy savings of 2% for every 50-hp motor.
Compressed Air
Compressed air is used for machine power, air tools, and pneumatic valves. Common improvements to these systems include repairing leaks in piping and equipment, reducing the output pressure, using a cold-air intake, setting up remote air receivers, identifying areas with large pressure drops, controlling the loading pattern of the system, and reducing inappropriate uses. More costly solutions include proper sizing and distribution of the system, improving sequencing controls, and installing variable speed compressors.
Process Heating Systems
In facilities with painting, annealing, and plating operations, process heating comprises a significant amount of facility gas and electric use. Potential technology improvements include better insulation, heat recovery from furnaces, reduced cycle times, and minimized soak or stabilization periods. Computerized controls for ovens may help reduce energy use. Plating and metal finishing baths should be inspected for pipe and tank insulation, as well as proper fitting covers, which can minimize heat losses from the tanks. Automated cover systems may prove operationally and economically beneficial based on energy costs. Upgrading chemical technology in plating and metal finishing can allow lower bath temperatures.
For additional assistance identifying energy efficiency opportunity in your facility, contact:
Daniel Chang – Associate Engineer
612-624-0808
dwchang@umn.edu
Optimizing Water Usage in Metal Fabrication
Managing water use in complex operations with rigorous process requirements can be a difficult challenge. Choosing the quality of water you are going to use has varying cost and process implications. Optimizing well water, city water, softened or deionized water use has implications for treatment chemical use levels, discharge volume and facility effluent composition. Inefficient use of water can add up to unnecessary cost to your process.
One example for managing water use is choosing the correct spray nozzle and flow rate. Using a more efficient sprayer will greatly reduce the volume of water and that reduced water use can result in additional resource use reductions. A 2016 MnTAP Intern Project at Nordic Ware saved over 9 million gallons of water annually. Foaming in the first stage of a cleaning system was reduced by standardizing spray settings based on part weight, implementing spray nozzle maintenance procedures, and converting the make-up water from soft water to city water. These recommendations along with other washer optimization actions saved the company over 9 million gallons of water, 28.5 tons of salt from water softening and $86,000 annually.
Daniel Chang – Associate Engineer
612-624-0808
dwchang@umn.edu
Funding Opportunities
Business Pollution Program Offers Increased Support for Businesses
Ramsey County’s Business Pollution Prevention Program is now offering financial support to dry cleaning, auto body, and painting businesses in Ramsey County to adapt to safer and more efficient technology.
As many businesses have seen reduced business during the COVID-19 pandemic and are facing economic hardship, the Business Pollution Prevention Program is now offering increased support to dry cleaning, auto body, and painting businesses in Ramsey County to adapt to safer and more efficient technology. The program offers financial support for up to 75% of project costs, up to $50,000, for businesses to upgrade their equipment to reduce pollution and improve the health of workers, communities, and the environment. For more information, contact Christina Vang at cvang@environmental-initiative.org.
MPCA Loans to Help to Reduce TCE
The MPCA has made up to $250,000 for small businesses to switch from using TCE to a safer alternative. The Small Business Environmental Improvement Loans are available at zero-percent interest for equipment purchases and installation associated with a switch from TCE. Eligible projects will reduce air emissions through switching from the use of TCE to an alternative demonstrated to be less toxic.
See the MPCA website to Learn more