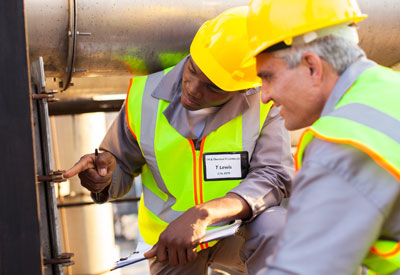
Many companies have employed the team structure and have realized significant waste and energy use reductions as well as cost savings due to the nature of the team. Many teams consist of members from all ranks of the company and all locations in the facility. This enables the team to tackle projects and get many points of view regarding solutions.
Engaging your staff in pollution prevention and energy efficiency teams may be beneficial to your facility. MnTAP can help develop an internal team designed to investigate your waste-related issues. Fill out our Team Application [PDF 52KB] and submit it to MnTAP to get started forming a team.
What to Expect
MnTAP’s process for forming internal pollution prevention and energy efficiency teams involves multiple steps that get your employees engaged and prepared. We recommend forming a team of staff members from multiple departments and management or non-management levels. After forming the team, MnTAP can provide training on effective teamwork, pollution prevention, energy efficiency, and moving forward with implementation. MnTAP staff members can continue to meet with your team regularly for up to a year to help facilitate discussion, provide engineering expertise, and identify opportunities for implementation.
Benefits to the Company
Your facility can benefit from empowering a team of employees to address your pollution prevention or energy efficiency concerns. Teams are a great tool to use because:
- The structure encourages employees from all areas of the facility to be involved.
- Teamwork drives creativity and results in numerous possible solutions.
- Teams build continued support for pollution prevention and energy efficiency solutions among employees.
Example: Pepsi Bottling Group Team
Pepsi Bottling Group (PBG) formed an energy efficiency team in the fall of 2008 to reduce energy use throughout the facility and meet their 2009 goal. MnTAP provided technical guidance and team facilitation. The PBG team and MnTAP worked together to recognize energy saving projects that had previously gone unnoticed. The team found energy reduction opportunities through improving heat exchangers and reconnecting their drying dispenser, which saves them $1,000 each year. This and other energy efficiency team efforts lead to cost savings of approximately $14,000. A Source article was published in 2009 and provides more information on the success of the team at PBG.
Additional Resources
- Articles: How to Conduct a Treasure Hunt. GreenBiz.com took an in-depth look at how companies are conducting rigorous treasure hunts for energy efficiency projects. This blog entry provides a step-by-step primer to help your firm get started with energy efficiency teams.