Pollution Prevention & Energy Efficiency for Iron Mines
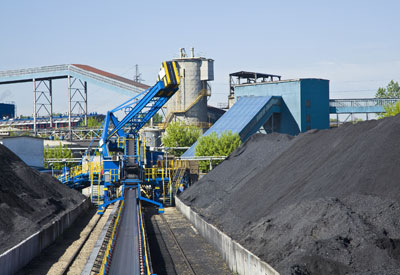
Northeast Minnesota’s six active iron mines and their processing facilities produce two-thirds of the iron ore used to make steel in the United States. The iron ore is recovered from taconite, which is a challenging process that produces large amounts of waste and requires significant energy use. Typical waste streams include priority pollutant air emissions, cooling water, wastewater, and waste rock as solid waste. Additionally, all six mining facilities in Minnesota are high energy users, according to the U.S. Department of Energy (DOE). Total energy use is estimated at 25 million mmBtu annually.
Energy Efficiency Opportunities
To make mining more efficient, the U.S. mining industry partnered with U.S. Department of Energy, Office of Energy Efficiency and Renewable Energy (EERE)to complete a number of tasks including developing an energy analysis to identify energy-saving opportunities. about these efforts.
Through a U.S. Department of Energy–sponsored project, MnTAP facilitated compressed air audits at United Taconite and Hibbing Taconite. From that project, MnTAP learned that facilities have common opportunities for energy efficiency improvements: leak reduction, storage, sequencing, and removing inappropriate uses such as cooling bearings and cleaning conveyor belts. A fact sheet, Air Compressor Energy-Saving Tips, is available to help your mine save energy.
A number of energy intensive mining processes are similar to processes in other sectors:
Resources
MnTAP offers the following case studies as examples of ways that mines can improve processes, reduce waste, and lower energy use. Additionally, we provide a list of mining industry associations that provide support and networking opportunities to iron mines.
MnTAP Intern Projects and Resources
- Summary: Hibbing Taconite Company (2001). The company saved $260,000 by reducing ore spills by 75% (19,000 tons) through changes to equipment and maintenance schedules.
- Water Conservation
DOE Industrial Technologies Program Assessments: Assessment results from other types of mining may identify areas of opportunity for iron mines
- Case Study: Coeur Rochester, Inc. [PDF 299KB]. A plant-wide assessment of Nevada Silver Mine found opportunities to improve process control and reduce energy consumption.
- Case Study: Kennecott Utah Copper Corporation [PDF 306KB]. This facility used energy assessments to identify $930,000 in potential annual savings.
Mining Industry Associations
- Iron Mining Association of Minnesota promotes Minnesota’s iron ore industry.
- National Mining Association represents the interests of mining before Congress, the Administration, federal agencies, the judiciary, and the media.
Other Resources
- The Coleraine Minerals Research Laboratory also offers assistance to Minnesota’s iron mines. This facility is at the University of Minnesota-Duluth in the Center for Applied Research and Technology Development.
- Iron Range Resources
This Web site has information to advance regional growth of Northeastern Minnesota’s mining areas.