Waste Reduction in Plating Processes
Overview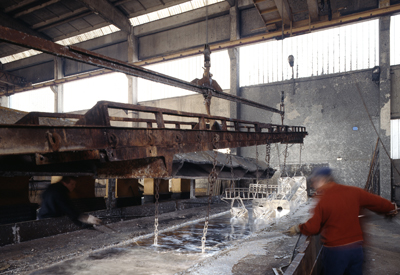
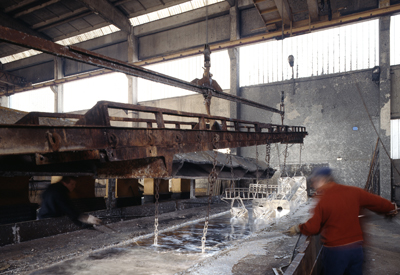
The process of plating metals often includes hazardous materials like heavy metals, strong acids, strong bases, and cyanide. Many of the metals and chemicals associated with plating have significant environmental effects as well as human health effects, which require significant maintenance and regulation. Waste reduction can be accomplished in a number of ways: dragout reduction, bath concentration control, bath life extension, and alternative chemistries.
Dragout Reduction
Dragout reduction involves a number of methods that keep plating chemistries in the plating bath. These methods are illustrated in a video, Pollution Prevention for Metal Platers: Dragout Reduction, from the California Department of Toxic Substance Control, and include:
- Use slow withdrawal speeds to allow bath surface tension to help pull liquid off parts as they are withdrawn.
- Allow time for parts to stop or greatly slow dripping before they are moved to the next bath. 10 to 30 seconds of drain time is generally adequate, but will vary by part design and loading, barrels take longer than racks to drain.
- Improve fixturing equipment and procedures. Orienting parts for drainage can greatly reduce dragout, especially parts with holes, threads and cupped designs. Rack design and loading procedures affect the drainage orientation. Good rack design should stagger parts so dripping from one part onto the part below is minimized. Barrel design [PDF 2.4MB] also greatly affects drainage – some designs drain much quicker than others.
- Rinsing can reduce dragout. Low volume atomized spray rinsing above the process tank can wash most concentrated chemical films off parts and back into the plating tanks without adding significantly to tank levels. This works best when evaporation losses require additions to maintain levels, but can be used in other situations if losses and additions are balanced.
- Bail back concentrated plating solution from a dead rinse back to the plating tank when additions to maintain plating tank levels are needed. This works best for hot plating tanks, and where contaminant build-up is not an issue.
Bath Concentration Control
Keeping chemical concentrations to the minimum level needed for adequate performance means that less chemistry will be lost to dragout. Bath concentrations should be monitored and maintained. Additions should be measured to match the need and addition pumps can be used to make slow additions over time to avoid concentrations swings. Avoid making chemical additions to solve plating quality issues unless it is known that chemical depletion is the cause. For barrel plating, consider to options for adding fresh solutions to the barrel rather than waiting for solutions to diffuse and exchange through the sides of the barrel. Contacting parts with fresh solution allows lower concentrations and may speed up the plating process.
Bath Life Extension
Making process baths last longer saves chemicals. Know what causes chemistries to go bad and address those causes. Filter baths to reduce particulate build-up. Skim impurities off the bath surface. Remove parts that have fallen off racks that may continue to react with bath chemicals. Use de-ionized water to make-up plating and process baths to avoid the buildup of hard water salts, especially in baths operated at elevated temperatures. Consider batch treatment of baths to precipitate contaminants without replacing the bath – acid etches are one where there are claims of effective batch treaments.
Alternative Platings and Solutions
Switching to alternative plating chemistries can reduce hazardous discharges, treatment costs and environmental reporting and can also reduce your employees exposure to hazardous materials. The plating type is generally set by customer specifications. For hexavalent chrome plating various forms of cyanide plating talk with your customers about alternative plating chemistries that might serve them better. See the fact sheet from the Environmental Sustainability Resource Center for the listing of a number of alternative plating chemistries.
Resources
-
ISTC Reports: Pollution Prevention for the Metal Finishing Industry: A Manual for Pollution Prevention Technical Assistance Providers. A 1997 report by the Illinois Sustainable Technology Center & NEWMOA, covers cleaning, rinsing, plating and other metal deposition processes as well as facility design.
- EPA Report: Innovative Cooling Systems for Hard Chrome Electroplating [PDF 100KB]. This fact sheet provides a summary of chrome emission regulations, information on external cooling systems for hard chrome electroplaters, and the benefits of implementing such systems.
- MnTAP Reference List: Centrifuge Equipment and Services (2011). Centrifuges are generally used for liquid-solid phase separation; this list provides information on suppliers of centrifuge equipment and services.
- MnTAP Intern Summary: Technical Plating Saves Over $45,000 by Reducing Water and Sewer Costs (2003). Technical Plating improved flow control on one plating line and effluent reuse and reduced water demand by 2,625,000 gallons per year, saving $7,100 a year plus $44,100 in one-time SAC fees.
- California DTSC video: Pollution Prevention for Metal Platers: Three Case studies. Three southern California businesses demonstrate equipment that reduces their waste and operating costs.
- Case 1: Reverse Osmosis for Metal Finishing (at 1:25 minutes into the video).
- Case 2: Cooling Systems for Hard Chrome Electroplating (at 7:35 minutes into the video).
- Case 3: Reducing Rinse water Use With Conductivity Control Systems (at 14:55 minutes into the video).