Basic Steps of an Energy Assessment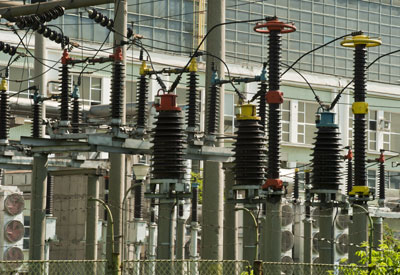
Developing a detailed energy analysis of your facility can help you initiate an energy conservation program. An energy analysis consists of two phases: acquiring and analyzing data. Acquiring data helps quantify energy flows into a facility, energy use and energy purchase costs. Analyzing data identifies energy efficiency opportunities. These opportunities can be prioritized based on cost and business activities. Implementing them will reduce energy use and save money.
Assessment Procedure
The following is intended as a general guide for starting an energy assessment at your company. More detailed information can be obtained from The Self Assessment Workbook for Small Manufacturers, Rutgers University Industrial Assessment Center.
1. Analyze energy inputs
Collect gas, electric and other utility bills for the previous one to two years. Graph the data to identify any trends. If gas and electric are the main energy sources, try graphing monthly kilowatt and kilowatt-hour use for electricity and British thermal units (Btus) for gas use. It might be helpful to also graph monthly gas or electric costs.
2. Understand the utility bill
Your utility’s rate structure is key to understanding how energy is billed. This information can be obtained from your utility. For gas or liquid fuels, the rate is generally on a per-unit-volume (gallon or cubic feet) or thermal content (therm or BTUs in case of natural gas). Electricity is generally more complicated. In Minnesota, medium-sized facilities are commonly charged a rate based on a variety of factors. In addition to the simple energy charge for the amount of energy used, rates may include the demand charge (could vary seasonally), power factor adjustment charge, resource adjustment fees, service fee, Conservation Improvement Program fees and sales tax.
3. Gather process or industry specific information
Obtain as much of the available information as possible to help you understand your operation and identify key focus areas. Process specific information might be readily available from equipment vendors, suppliers or organizations such as the Electric Power and Research Institute (EPRI) and the Gas Technology Institute (GTI). The U.S Office of Energy Efficiency & Renewable Energy web page is an excellent source of energy efficiency information for many large industries and/or specific high energy-consuming equipment.
4. Gather plant specific information
Geographic location, weather, facility layout, hours of operation and the equipment list affect energy use. Understand the key safety issues of a facility before gathering information on the plant floor.
5. Conduct a plant walk-through
Conduct a general walk-through of the facility to get a basic overview of the major equipment. After the walk through, follow up with the equipment operators to get more detailed information on how and when the equipment is run.
6. Gather detailed data
Gather enough information on air compressors, HVAC, lighting, motors, specialized equipment and other equipment to estimate annual energy use. The data will help identify key energy efficiency opportunities. Obtaining useful data might depend on access to specialized tools such as a combustion analyzer, light meter, ultrasonic air leak detector and watt meter.
- Electric motors. Inventory all motors above one horsepower, prepare a data sheet on size and operating specifications (such as full load amperage and average load), age, operating hours and power factor. For more information on motors see the MnTAP fact sheet Motor Basics.
- HVAC. Inventory all HVAC equipment and collect data on unit specifics like energy use, operating hours and age.
- Lighting. Inventory light fixtures and lamps, wattage and hours of operation, note tasks performed in various areas to validate lighting level requirements, identify areas of infrequent use. For more information on lighting see the Lighting Basics page.
- Peak equipment loads. Identify infrequently used equipment or equipment that could be used during off-peak times.
- Waste heat sources. Low-grade waste heat has the potential to be used in a variety of applications including supplying building heat (winter) or preheating water for warm or hot water requirements. Identify all sources of waste heat—air compressors, air conditioners, boilers and heaters, cookers, furnaces, ovens, process cooling systems, etc. Measure flow rates and temperatures of waste heat sources. For more information on lighting see the Heat Sources page.
- Water heaters. List fuel type and rate of energy use, where the energy is used, daily demand and temperature requirements.
7. Generate a list of energy efficiency opportunities
Identify energy efficiency opportunities for all operation areas in the plant. Estimate the energy savings of proposed ideas and calculate a cost comparison.
8. Generate an action plan for implementation
Prioritize energy efficiency opportunities based on cost and facility work schedule. Set up a program to implement opportunities and continually look for new opportunities.
Resources
- U.S. DOE Advanded Manufactering Office Best Practices: Software Tools. The Advanced Manufacturing Office (AMO) offers free software tools to help you identify and analyze energy system savings opportunities in your plant or industrial facility.
- U.S. DOE: Better Business Better Plants Program. The Better Plants Initiative has advanced proven efficiency solutions by challenging market leaders to accelerate the pace of energy efficiency adoption, highlighting partner success stories and industry best practices, and encouraging the latest technological innovation.
- Analysis Tool: Business Analyzer. Developed by Energy Guide, this tool helps you conduct a self-guided, energy-efficiency analysis of your business.
Case Studies
The following case studies highlight assessments conducted through the U.S. DOE Save Energy Now Program. More case studies and information can be found on the Office of Energy Efficiency and Renewable Resources Web site.
- U. S. Steel’s Taconite Pellet Manufacturing Facility Improves Process Heating Efficiency [PDF 598KB]. The facility implemented projects to total $760,000 in annual energy cost savings and 95,000 MMBtu in annual gas use.
- Boise Inc. St. Helens Paper Mill Achieves Significant Fuel Savings [PDF 527KB]. After implementing recommendations from the audit, the facility achieved annual energy cost savings of more than $1 million and annual fuel savings of approximately 154,000 MMBtu.
- Energy Assessment Helps Kaiser Aluminum Save Energy and Improve Productivity [PDF 636KB]. The plant in Sherman, Texas, improved its annual furnace energy intensity by 11.1% after implementing recommendations from the assessment.