Energy Efficiency Opportunities for Ferrous Metal Casters
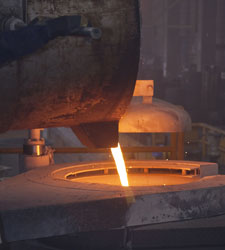
Inefficiencies in melting may be found in stack losses, inaccuracies in temperature measurement, conduction and radiation losses, poorly-fitting charge well covers and doors, temperature imbalance when adding cold metal to the charge and improper handling procedures. Process heating and compressed air systems are two areas that may hold efficiency improvement opportunities.
Process Heating
Melting and molten metal holding technologies comprise a large portion of energy consumption in the primary metals industry. Fuel-fired melting system opportunities from MnTAP’s experience includes:
- Insulation integrity and maintenance
- Proper metal furnace charging and fluxing procedures
- Process flow optimization
- Ladle preheating
- Burner tuning
- Furnace and ladle covers
- Waste heat recovery technologies like recuperative and regenerative heat exchangers or combined heat and power applications
When considering new furnaces or ovens, it is important to note that there are a number of types of melting furnaces on the market and each have differing degrees of efficiency that can affect the degree of metal loss and thermal efficiencies.
Furnace Type | Gas | Electric | Melt Loss | Thermal Efficiency | Thermal Efficiency Rating |
---|---|---|---|---|---|
Crucible (gas) | X | 4 – 6% | 7 – 19% | POOR | |
Cupola | X | 3 – 12% | 40 – 50% | GOOD | |
Reverberatory | X | 3 – 7% | 30 – 45% | FAIR to GOOD | |
Rotary | X | 35% | FAIR | ||
Stack melter | X | 1 – 2% | 40 – 45% | GOOD | |
Direct Arc | X | 5 8 % | 35 – 45% | FAIR to GOOD | |
Induction | X | 0.75 (aluminum) – 3% | 50 -76% | GOOD to EXCELLENT | |
Reverberatory | X | 1 – 3% | 59 – 76% | EXCELLENT |
Electric melting has some overall advantages in thermal efficiencies and in lower metal melt loss. Combustion inefficiencies, exhaust waste heat loss, and combustion and oxidation contaminants in the form of dross and slag metal melt loss can contribute to fuel-fired furnace lesser efficiencies. Nonetheless, fuel-fired furnace equipment operations can effectively employ a variety of procedures and methodologies that can lead to some significant energy savings estimates.
Resources
- DOE Report: Advanced Melting Technologies: Energy Saving Concepts and Opportunities for the Metalcasting Industry [PDF 1.8MB]. The study examines current and emerging melting technologies and discusses their technical barriers to scale-up issues and research needed to advance these technologies, improving melting efficiency, lowering metal transfer heat loss, and reducing scrap.
- DOE Fact Sheet: Efficient Process Heating in the Aluminum Industry [PDF 285KB]. Aluminum producers can cut process heating energy use 10 to 30% by improving operations in five areas: heat generation, heat transfer, heat containment, waste heat recovery and enabling technologies.
- DOE Report: Energy Use in Selected Metal casting Facilities – 2003 [PDF 729KB]. This report provides an energy benchmark for various metal casting processes. It describes process flows and energy use by fuel type and processes for selected casting operations. It also provides recommendations for improving energy efficiency in casting.
- DOE Tip Sheets: Process Heating. These tip sheets give engineers, technicians, equipment operators and others technical advice to improve process heating systems.
- DOE Article: Seven Ways to Optimize Your Process Heat System [PDF 24KB]. This one-page article outlines best bets for process heat system savings and improvements.
Compressed Air
Compressed air is a very expensive and energy-intensive utility commonly used for air tools and control valves, as well as occasionally for drives, media blasting, cooling, and blow-offs. Common improvements include repairing leaks in piping and equipment, reducing the compressor output pressure, using a cold-air intake, setting up remote air receivers, correcting large system pressure drops, controlling the loading pattern of the compressed air system, and reducing inappropriate uses such as process cooling and cleaning. More costly solutions include properly sizing and distribution of the compressed air system, improving sequencing controls, and installing variable speed compressors to handle variable loads.
Resources
- MnTAP Fact Sheet: Air Compressor Energy-Saving Tips. This fact sheet will help you calculate operating costs, understand your system and identify easy-to-implement energy efficiency strategies for your compressed air system.
- DOE Tool: AirMaster+ Software. This assessment and analysis software package helps maximize the efficiency and performance of compressed air systems through improved operations and maintenance practices.
- MnTAP Source Article: Top Compressed Air Energy Saving Options (pg 3). Compressed air assessments reveal that facilities have common opportunities for energy efficiency improvements: storage, sequencing, and removing inappropriate uses.
Energy Case Studies
- MnTAP Intern Summary: QX Inc. (2006). The intern evaluated how to reduce energy use in the melt furnace operation and recover heat from the evaporator system.
- DOE Summary: AMCAST Industrial Corporation [PDF 212KB]. A plant-wide energy assessment led to the identification of 12 projects that have a combined potential annual savings of $3.7 million and a three-month payback.
- DOE Summary: Compressed Air System Improvement Project Saves Foundry Energy and Increases Production [PDF 187KB]. In the late 1990s, Indianapolis Casting Corporation optimized its compressed air system to save $395,000.
- DOE Summary: Ford Cleveland: Inside-Out Analysis Identifies Energy and Cost Savings Opportunities at Metalcasting Plant [PDF 265KB]. Sixteen projects were identified at this facility and have a combined potential annual savings of $3.3 million, along with two longer-term projects that would save an additional $9.5 million.
- DOE Summary: Metlab Plant-Wide Assessment [PDF 639KB]. As a result of the plant-wide assessment, Metlab has prepared a plan that will produce an annual savings of approximately $528,400.
To learn more about energy-efficient metal casting technologies, visit the Department of Energy (DOE) Advanced Manufacturing Office’s, formerly Industrial Technologies Program, web site. The AMO has sponsored many collaborative R&D projects for the metal casting industry; many of which have produced technologies that are now commercially available. Other projects focused on identifying emerging technologies.