Healthcare Hazardous Waste (RCRA Waste)
Why do we care about RCRA hazardous waste?
What types of facilities generate RCRA waste
What are the 10 steps to RCRA waste compliance
Infectious waste & hazardous waste are not synonymous
Regulatory consensus on health care issues (MPCA document)
Facility & cleaning related chemicals
Hazardous waste disposal companies
Overview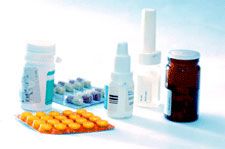
If you work in a healthcare facility of any kind, chances are you produce some amount of hazardous waste. Hazardous waste refers to any waste that is regulated by the Resource Conservation and Recovery Act of 1976. Known widely as RCRA (pronounced “wreck-ra”), this act from the Environmental Protection Agency (EPA) establishes rules for a “cradle to grave” system of governing hazardous waste from the point of generation through disposal. At the federal level, strict rules govern accumulation, treatment, storage, disposal, manifesting, and record-keeping for these wastes.
In Minnesota, the Pollution Control Agency (MPCA) is the governing body for RCRA hazardous waste. In the Twin Cities metropolitan area, seven counties (Anoka, Carver, Dakota, Hennepin, Ramsey, Scott, and Washington) are responsible for RCRA regulation in their counties. Keep in mind that the information provided on this webpage is written for a Minnesota-wide audience; the rules are the same for any county in Minnesota, but if you are in one of these seven metro counties, you would obtain your licensing from the county regulators as opposed to the state regulators. For more information on licensing, please view Steps 2 and 3 of the section “What are the 10 steps to RCRA waste compliance?” below.
In brief, the hazardous wastes covered by RCRA include any chemical or substance found on one of these lists:
- Commercial chemical products, listed with the code “P” or “U.” Healthcare examples of P-listed waste include warfarin, nicotine (excluding over-the-counter nicotine replacement therapies such as patches, gum and lozenges), and physostigmine; U-listed examples include mitomycin and phenol. Note that P-listed wastes are considered “acutely toxic” and may also be referred to as “acute hazardous wastes,” with special collection and disposal rules.
- Hazardous wastes from specific industries/sources, listed with the code “K.” Healthcare facilities typically do not generate K-listed waste.
- Hazardous wastes from nonspecific sources, listed with the code “F.” Healthcare examples include solvents such as acetone, methanol, and xylene (chemicals typically found in a laboratory).
- Materials that exhibit a hazardous waste characteristic (ignitability, corrosivity, reactivity, or toxicity), designated with the code “D.” Healthcare examples include dexamethasone, silver nitrate applicators, thimerosal, influenza vaccines, and human insulin.
- Minnesota uses an additional category of waste called the lethality characteristic (MN01) which greatly impacts healthcare. More information on the lethality characteristic as it relates to healthcare can be found on the pharmaceutical waste topics
The MPCA maintains an updated list called the Regulatory Consensus on Health Care Issues. It is a detailed document that speaks specifically to the healthcare industry. This document is discussed in greater detail below.
Why do we care about RCRA hazardous waste?
There are very compelling environmental reasons to care about the proper disposal of RCRA waste. If not disposed of correctly, RCRA wastes can (and do) wreak havoc on our ecosystems. A major issue with incorrect disposal of pharmaceuticals and other RCRA wastes is the leaching of these materials into groundwater. Groundwater becomes contaminated with non-organic chemicals, which can change the composition of the surrounding ecosystem.
Some wastes clearly need to be managed in a specific way; for example, we wouldn’t pour a gallon of gasoline into a hole in our backyard. However, proper management isn’t always so clear when it comes to pharmaceuticals and personal care products (often called PPCPs). PPCPs are defined by the EPA as “any product used by individuals for personal health or cosmetic reasons or used by agribusiness to enhance growth or health of livestock” and include “a diverse collection of thousands of chemical substances, including prescription and over-the-counter therapeutic drugs, veterinary drugs, fragrances, lotions, and cosmetics.”
Healthcare facilities contribute to the problem of PPCPs in our ecosystems when they:
- Throw pharmaceuticals and other RCRA wastes into the regular trash
- Throw pharmaceuticals and other RCRA wastes into the infectious waste stream
- Flush pharmaceuticals and other RCRA wastes down the sewer drain
Scientific research shows that sewage systems are not equipped to remove PPCPs from human waste water. This means that once PPCPs enter the water, they tend to stay in the water, slowly changing aquatic ecosystems. Similarly, landfills (for trash) and autoclaves (for infectious [biohazard] waste) cannot prevent the leaching of substances into groundwater, so wastes that enter either of these waste streams has the potential to seep into our streams, lakes, and rivers. As of August 21, 2019 federally-regulated pharmaceutical hazardous wastes may not be sewered for disposal (40 CFR 266.505). Both the EPA and USGS have informational resources on this topic. The MPCA also keeps detailed information about Minnesota’s impaired waters. For additional resources, visit the case studies, resources, and links section of this web page.
On a final note, there are major issues with regard to the overuse of antibiotics (both prescribed and in our livestock) and the overuse of antibacterials (found in our personal care and cleaning products). Rigorous medical research indicates a marked increase in multi-drug resistant organisms (MDROs); the more non-therapeutic exposure humans have to antibiotics, the more problems we may be creating in terms of “superbugs” such as c. Difficile and MRSA.
For these reasons and more, it is incredibly important for healthcare facilities to comply with all RCRA waste rules and to maintain awareness of the amount of antibacterials and antibiotics used and prescribed. MDROs, antibiotics, and their harm on humans are discussed in greater detail on our infection prevention webpage.
Which types of healthcare facilities generate RCRA hazardous waste?
The information on this page is relevant for any business that provides direct patient care. Examples include hospitals, nursing homes, surgery centers, outpatient family practice clinics, specialty clinics, dental clinics, veterinary clinics, imaging and radiology clinics, orthopedic and physical therapy clinics, acupuncturists, chiropractic, clinical laboratories, and stand-alone pharmacies. MnTAP does not provide guidance for medical manufacturers or other healthcare industry partners at this time.
The MPCA began enforcing RCRA rules at Minnesota hospitals around the mid-2000s and at non-hospital healthcare facilities around 2009. Since that time, most healthcare facilities have come into compliance, but we realize that for various reasons, including staff turnover and building moves and construction, facilities may need to review their hazardous waste management process starting from “step 1.” This is where the ten steps to compliance come into play, which is discussed in detail below. If at any time you are worried that your facility is out of compliance with RCRA laws, please call the MnTAP offices at 612-624-1300, and we will gladly provide over-the-phone technical assistance or visit your site to help you come into compliance with RCRA waste laws.
There are four categories of hazardous waste generators. Your facility will fall into one of these categories. Your category dictates your training, storage, and other requirements related to RCRA waste.
What are the 10 steps to RCRA waste compliance?
The MPCA makes it easy to stay in compliance with RCRA waste laws; they maintain guidance documents for all 10 steps of compliance. Though they are not geared toward healthcare specifically, the documents do a great job of walking through the steps required to ensure compliance with the law. Keep in mind that there are stiff penalties and fines for noncompliance with RCRA laws; the MPCA, the seven counties, and even the federal EPA all have the legal right to enter your facility at any time to perform unannounced inspections. The best way to avoid a fine is to ensure you are in compliance with the law at all times.
The section below outlines the basic steps required for compliance in Minnesota, as well as a short description of what each step means for your healthcare facility. Please visit the MPCA 10 steps to compliance page to access a full PDF document explaining each step below in greater detail.
-
- Step 1: Evaluate your waste and determine your generator size
Evaluating your waste means identifying any substance used on-site that is Listed (P, U, K, or F-list or regulated polychlorinated biphenyl (PCBs)), is D-listed or Characteristic (ignitability, oxidizers, corrosivity, reactivity toxicity, lethality), or is an MN01 lethal waste. You can either assume all waste is hazardous or evaluate the waste as non-hazardous within 60 days of generation. To evaluate a waste, you may either evaluate by knowledge or by laboratory analysis and must keep the evaluation documentation on hand for at least three years after you stop generating the waste. For assistance evaluating your waste stream, the University of Minnesota’s Department of Health & Safety maintains a searchable database that will tell you whether a specific chemical or pharmaceutical is hazardous. The database may not contain everything you use, but it is a useful tool for performing quick searches on relatively common products. - Step 2: Determine Your Generator Size
You can based on the volume and types of products you use each month. Please note that the state of Minnesota has more stringent generator size requirements than the Federal Regulations, so refer to MPCA documentation on generator status guidance. Most healthcare facilities are Very Small Quantity Generators (VSQG) or Small Quantity Generators (SQG). Large hospitals are likely Large Quantity Generators (LQGs) and may require extra assistance. Please note, there are hazardous wastes that might not count toward your generator size (i.e., PCBs) but still need to be reported to MPCA or Metro County.The four categories for hazardous waste generators are as follows:
-
- Minimal Quantity Generator (MiniQG) = less than 100 pounds total of hazardous waste per year and no acute hazardous waste (not all counties in the metro area accept this designation)
- Very Small Quantity Generator (VSQG) = less than 220 pounds per month of hazardous waste and less than 2.2 pounds per month of acute hazardous waste
- Small Quantity Generator (SQG) = between 220 and 2200 pounds per month of hazardous waste generated and less than 2.2 pounds per month of acute hazardous waste
- Large Quantity Generator (LQG) = more than 2200 pounds per month of hazardous waste OR more than 2.2 pounds per month of acute hazardous waste generated
-
- Step 3: Obtain your hazardous waste identification number (HWID), also known as your EPA ID
Any business in Minnesota that generates hazardous waste needs to obtain and maintain a HWID. This ID must be obtained for each physical address at which you operate your business. The HWID is free, and you do not need to do any annual upkeep unless you move or close your business. The MPCA is the governing body for the HWID (for all counties), and the form for obtaining your HWID is called the Notification of Regulated Waste Activity. You can also check to see if your site already has a HWID by following this link and searching by city or business name. - Step 4: Obtain your hazardous waste license (either from the state or from the seven metro area counties)
If you are located in one of the seven metro counties (Anoka, Carver, Dakota, Hennepin, Ramsey, Scott, or Washington), obtain licensure from your county. If you are located in any other county, obtain licensure from the state. Before obtaining a license, you will need to (1) evaluate your wastes, (2) establish your generator size, and (3) obtain a HWID. Licenses generally cost money (based on county and amount of hazardous waste generated) and must be maintained on an annual basis (all generators except for MSQGs, which report every three years). Part of the licensing process is to report to the state how much waste your facility generated in the prior year. It is crucial that you keep your hazardous waste shipping manifests; without them, you will be unable to fill out your annual licensing paperwork. You will also need to have chosen a hazardous waste disposal company to list on your licensing paperwork.
- Step 1: Evaluate your waste and determine your generator size
- Step 5: Learn how to label and accumulate (or ‘store’) your hazardous wastes
There are many rules around labeling and accumulating waste. For example, if you are placing an expired bottle of lab solvent into your hazardous waste storage area, it must be labeled with the words “hazardous waste” along with a description of the contents and the date it entered storage. You must also store hazardous waste with secondary containment (e.g. in a room without a floor drain or in a plastic container). Do not store incompatible wastes (such as acids and bases) close to one another. Perform weekly documented inspections of storage area. There are also requirements for hazardous waste at the point of generation, called satellite accumulation areas, and time limits on how long you can keep waste on-site. Detailed instructions on how to store, label, and manage your healthcare RCRA waste can be found in our Waste Training Toolkit.The majority of the updates to 40 CFR 266 Subpart P do not apply to Minnesotan businesses due to the more strict state regulations; however, there are differences in accumulation times for the different generator statuses that do apply. VSQGs may accumulate hazardous waste indefinitely up to a certain volume, but SQGs and LQGs are allowed to accumulate pharmaceutical waste up to 365 days.
- Step 6: Correctly treat and dispose of your hazardous waste
RCRA waste can be managed in a few ways. It can be recycled (though this is a difficult option for many healthcare wastes), or it can be transported to a Treatment, Storage, and Disposal facility (TSDF) by a hazardous waste disposal company or, in rare circumstances, by the generator using a business vehicle. The MPCA Step 6 compliance document should be consulted before any decisions are made about treatment and/or disposal. You can also find more information in the hazardous waste disposal companies section of this webpage. - Step 7: Document your hazardous waste shipments with manifests (shipping papers) from hazardous waste disposal companies
All RCRA waste shipments from your site must be accompanied by a formal shipping document, called a manifest. There are several signatures required on a manifest, and you, the facility, are ultimately responsible for any errors on the manifest, so it is crucial that you check your manifests carefully before signing them. One copy is kept at your site, one is kept by the disposal company, and one travels with the waste to the Treatment, Storage, and Disposal facility. In some circumstances, you may be required to mail photocopies of your manifests to the state or county regulators. Read the MPCA compliance document to ensure that you are following the rules for maintaining and mailing copies of the manifests.Please note – as of August 21, 2019, it is federally mandated to list PHRM code on manifest.
- Step 8: Plan for emergencies involving hazardous waste
Chemical and other hazardous spills can put your patients and staff in danger. The MPCA requires that you have a program in place detailing your plan for if and when an emergency occurs. Tips include having a spill kit and posting (and maintaining) an emergency contact list. The emergency planning required for a facility is based on generator status (links to planning for VSQGs, SQGs and LQGs). Large Quantity Generators will require more rigorous plans and procedures, and everyone is required to follow the OSHA rules around chemicals and worker safety. For more information on these OSHA rules, please visit the What does OSHA mandate in regard to worker safety section of our website. - Step 9: Train your employees
Training requirements for employees who generate or come into contact with RCRA waste vary and can be confusing for a healthcare facility to follow. All sites are required to provide OSHA training on chemicals, and most are required to provide at least some training on proper waste disposal. For your convenience, MnTAP has assembled an easy-to-use Waste Training Toolkit that is separated by MiniSQGs/VSQGs vs SQGs/LQGs. The MPCA also has online and in-person trainings available. - Step 10: Maintain hazardous waste records
Hazardous waste records must always be accessible during unannounced inspections. This means that they need to exist in paper form (such as in a binder) or be immediately accessible online. If you have one person assigned to hazardous waste compliance, make certain that multiple staff know how to locate these documents in case an inspection occurs while that person is away from the office. Records include any documents produced during the waste evaluation, copies of current licenses and the HWID, shipping manifests, employee training records, and weekly container inspection logs. Most records need to be kept for at least three years after the record is no longer active, but MPCA recommends that you keep hazardous waste records for the life of the business. More information can be found in the Waste Training Toolkit.
Infectious waste and hazardous waste are NOT synonymous
Infectious waste and hazardous waste are not synonymous. This is one of the most common mistakes made concerning healthcare wastes. For example, a facility may believe that it is following the law by placing unusable medications into a red bag or sharps bin, but this is incorrect under all circumstances. The infectious waste stream is intended for biohazard burdens, such as blood and body fluids, and the waste is often autoclaved (steam sterilized), compacted, and sent to a special landfill. The chemical properties of RCRA waste are not eliminated by the autoclaving process; therefore, autoclaving is an inappropriate and ineffective method for treating RCRA hazardous waste. Regulators will be diligent in the inspection process to ensure that you do not have medication waste leaving through your red bags or sharps bins, so it is critical that you understand the difference and manage your program accordingly. There is, however, one situation in which a waste can be “dual” waste (both infectious and hazardous), and it is discussed in the Dual Waste section of our website.
For more information on infectious wastes specifically, please visit the healthcare infectious waste section of this website or the MPCA factsheet on Infectious Waste.
Regulatory Consensus on Health Care Issues
The MPCA maintains a document called the Regulatory Consensus on Health Care Issues. It is a must-read for any facility that is managing hazardous waste in healthcare. The document speaks in healthcare language and is the only place to find a complete ruling on healthcare-related hazardous waste issues at the state level. The seven counties in the metro area also abide by the rulings in this document.
Pharmaceutical Waste Topics
Pharmaceuticals are a unique issue for healthcare facilities and are governed by a complex set of management and disposal rules. Many pharmaceuticals used in healthcare facilities are classified as hazardous waste once they become “inherently waste-like,” meaning expired, partially used, leaking, or nonreturnable. Please click here to access information about pharmaceutical waste, or use the drop-down menu below to find a specific topic of interest.
Please note, as of August 21, 2019, it is now federally prohibited to sewer (i.e., flushing or pouring down the drain to publicly owned treatment works (POTW)) of hazardous waste pharmaceuticals by ALL healthcare facilities (including MiniQGs and VSQGs) and reverse distributors. Discharge of these wastes to septic tanks, privately owned treatment works and federally owned treatment works is already prohibited in 40 CFR section 261.4(a)(1)(ii).
Common ways to collect and store pharmaceutical waste
“The Minnesota lethality characteristic” and the “alternative method” of evaluation
P-listed “acutely” toxic hazardous waste
Controlled substances (narcotics)
Infectious waste & hazardous waste are not synonymous
Facility-and cleaning-related chemicals
When thinking about the hazardous waste generated in your facility, you cannot forget about the facility-related and cleaning-related chemicals. For example, aerosols, unless completely empty, are hazardous waste due to their ignitable characteristics. Disinfectants are hazardous waste because they are considered a pesticide according to the EPA. (These items do not become hazardous waste unless you have expired or unused product in need of disposal. Once in need of disposal, the chemicals will need to be treated as RCRA hazardous waste.)
These general rules apply to all chemicals used at your facility:
- Chemicals must be evaluated for hazardous properties. Are they Listed (F, K, P, or U-listed or PCBs), D-listed or Characteristic (ignitability, oxidizers, corrosivity, reactivity toxicity, lethality), or on the MN01 list? See Step 1: Evaluate your waste.
- If deemed hazardous, then all expired or unusable products must be moved to the hazardous waste storage area for proper disposal.
- Once in hazardous waste storage, an item must be placed into secondary containment so that if there is a leak, it will stay contained.
- The container must be labeled with a description of the contents, the date it was moved to storage, and the words “hazardous waste.”
- The product(s) must not be stored with incompatible chemicals. For example, you do not want to store acids and bases next to one another.
Examples of facility-and cleaning-related chemicals that may be hazardous:
- Aerosol hand sanitizers (if not empty)
- Quaternary ammonia compounds (low level disinfectant)
- Motor oil
- Paint and paint thinner
- Lime-A-Way
- Degreasers
- Stainless steel cleaners
- Adhesives, epoxy, glues
- Bleach
- Floor strippers
- Drain cleaner
- Lubricants and sealants
Performing a chemical evaluation can help you determine what is hazardous in your facility and help you train staff in all departments on correct disposal procedures. It is not uncommon for healthcare facilities to perform an annual review of chemicals used; consider sending a blank spreadsheet/template to all supervisors who may use chemicals in their departments (especially maintenance, housekeeping, and laundry) and don’t forget to include places that may not always be at the top of your mind (the painting department, grounds crew, etc). If you have outside contractors doing this work, you should always ensure that they are removing products when finished with a job. If they don’t, the product becomes your responsibility to store and dispose of.
A chemical evaluation may look something like this:
Department | Product Name | Possible Hazardous Material Contents |
---|---|---|
Maintenance | 10W-30 Motor Oil | Petroleum |
Maintenance | Anti-Clog | Ethanol, ammonium, chloride |
Housekeeping | Bathroom Cleaner | D002 |
Maintenance | Big Orange | Cyclohexene |
Housekeeping | Clorox Bleach | D001 |
Maintenance | E lectro Contact Cleaner | Methylpentane, isopropanol |
Maintenance | E Vaporator Cleaner | Xylene sulfonate |
Housekeeping | HB Quat | MN01 |
Maintenance | Hydraulic Fluid | Petroleum |
Maintenance | Ice Block | Propylene glycol |
Maintenance | Insulating Foam | Isopropyl, ethylene glycol |
Maintenance | Kwik SEal Tub/Tile Caulk | Butyl acetate, ethylene glycol |
Housekeeping | Lice Killer | D001 |
Maintenance | Lime-A-Way | Phospheric acid |
Maintenance | Squeeky Degreaser | D-limonene, ethoxylate |
Housekeeping | Stainless Steel Cleaner | D001 |
Housekeeping | Virex Cleaner | MN01 |
Maintenance | WD-40 | D001 |
For more information on how to properly evaluate, manage, and store your facility and chemical wastes, please visit our Waste Training Toolkit.
Laboratory-related chemicals
Laboratories tend to create an enormous amount of RCRA waste. Numerous chemicals used in a laboratory must be properly managed for disposal. Laboratory waste from analyzers, calibrators, cleaners, reagents, stains, and test kits must be evaluated to determine whether they are hazardous. Chemical constituents, contaminants, and preservatives found in laboratory chemicals may be considered hazardous at very low levels. Product inserts may fail to disclose information about small amounts of preservatives and contaminants, even though the product may still be considered hazardous under RCRA or MN01 lethality laws. Due to the vast number of chemicals used in a clinical laboratory, you will likely need to have an expert evaluate your laboratory wastes to ensure you are in compliance with disposal; your hazardous waste disposal company should be able to provide this service to you.
When solutions are rinsed off slides or equipment and discharged into the sewer, the action is considered disposal. The solutions must be evaluated before they are diluted by the rinsing process, and generators who intend to discharge waste into a sanitary sewer must notify their publicly owned treatment works (POTW), also known as a wastewater treatment plant, before discharge. A common alternative is to use a staining rack placed over a tray so that you can easily collect the used stain for hazardous waste disposal.
Examples of hazardous waste in a clinical laboratory:
- Fixatives such as B-5 and Zenker’s are hazardous waste for the toxicity characteristic (mercury).
- Clinitest tablets (both unused AND used) are reactive, corrosive, and MN01 lethal.
- Parrafin/xylene is ignitable and listed as D001 and F003 and must be treated as hazardous waste.
- Wright’s stain is ignitable and listed as D001 and F003 and must be treated as hazardous waste.
- Ictotest tablets (both unused AND used) are corrosive and must be treated as hazardous waste.
- Hemocue Hgb cuvettes are reactive and must be treated as hazardous waste.
- Reagents such as “Solution A” are toxic and must be treated as hazardous waste.
Due to the large amount of information associated with clinical laboratories, please visit our Clinical Laboratory Waste webpage for more information.
Hazardous waste disposal companies
Though there are many companies who provide waste disposal to businesses in Minnesota, far fewer provide RCRA waste disposal services. Though MnTAP cannot endorse any specific company, we recommend that you keep the following points in mind when you are shopping for a RCRA hazardous waste vendor.
At a minimum, your RCRA disposal company should:
- Assist you in the waste evaluation process (helping you understand what is and is not considered a hazardous waste)
- Assist you with your annual licensing paperwork to ensure you have captured all you need in order to be compliant
- Be able to explain, in detail, their shipping process, as well as where the “final destination” (Treatment, Storage, and Disposal facility) is for your waste
- Use the federal uniform manifest for all of your hazardous waste shipments and allow you to inspect what they have collected
- Be suggesting ways to save you money, such as bulking your waste and accumulating wastes for a longer period of time to avoid excessive transportation fees
- Be very clear about how they price your waste shipments (you should never encounter hidden or unexplained fees from your RCRA waste vendor)
- Provide over-the-phone or on-site technical assistance with someone in their company who understands RCRA regulations, especially as it relates to healthcare
- Care about the environmental and ecosystem impacts of healthcare waste and be interested in helping you minimize the amount of hazardous waste you generate
If you are not getting this type of service from your hazardous waste disposal company, you may want to shop for a different company. Hennepin County maintains a list of hazardous waste disposal companies in the metropolitan area, and many of these companies also provide service in Greater Minnesota. Remember, YOU have ultimate responsibility for proper disposal of your waste. If you send something through a vendor who then ends up doing something inappropriate with the waste, it is not them, but YOU, who are liable for the violation. Under law, YOU are responsible for understanding exactly where your waste is going at all times, with no exceptions.
Environmental best practice for managing RCRA hazardous waste
The most important thing to remember with RCRA laws is that they are intended to keep our environment and communities cleaner and safer from hazardous waste exposure. The number-one thing you can do to be environmentally conscious about RCRA waste is to follow the law! If every healthcare facility in Minnesota threw “just a little” in the trash, it would quickly add up. Staying diligent about your hazardous waste program is critical for the health of your patients, your community, and the ecosystems that surround you.
Here are several more tips for minimizing your environmental footprint with regard to your RCRA wastes:
- Choose to manage all unused portions of pharmaceuticals as RCRA hazardous waste.
This means that all of your pharmaceutical waste will be incinerated, as opposed to some reaching the landfill. Note that by doing this, you could enter a higher generator status. Thus, you may want to discuss this with your hazardous waste disposal company to see if they offer segregated collection of “hazardous” pharmaceuticals and “non-hazardous” pharmaceuticals – many do. - Rotate your pharmacy stock so that you end up with fewer out dates.
The best way to do this is to perform an evaluation of which medications are being used in which places in your facility, and keep an eye on which drugs are commonly expiring. Is something being used infrequently in one department and very frequently in another? If so, move items that are closing in on their expiration date to a location where they will be used more quickly. MnTAP performed an intern study on this topic; more details can be found here: Reducing Pharmaceutical Waste - Make your pickups count.
If your hazardous waste disposal company is coming to your site on a weekly basis, this is likely far too often, resulting in higher costs for you and a higher carbon footprint from the trucks. With correct storage practices, facilities large and small can often get by with only a few pickups per year (large quantity generators may require more, depending on the type of waste generated). Discuss this with your hazardous waste disposal company to see what schedule makes sense for your facility. Refer to Step 5: Learn how to label and accumulate (or ‘store’) your hazardous wastes for information on how long and what volume your facility can accumulate based on generator status. - Advocate for smaller medication vials.
You may be surprised to learn that pharmaceutical companies sometimes offer a larger vial of medication at a lower price than a smaller one. Unfortunately, this means that you, the customer, get stuck with leftover medication in your vials that you never actually needed in the first place (lidocaine is a great example of this). Begin to keep a tally of what you are finding in your RCRA waste stream and ask your pharmacy or purchasing staff to request a meeting with your pharmaceutical reps so that you can discuss ways to bring down the cost of smaller medication vials. You may also be able to take advantage of multi-dose vials, depending on the type of medication and the frequency of use. - Keep all “other” trash out of the RCRA waste stream.
It is far too common for facilities to throw empty medication vials into the RCRA waste stream, when empties actually belong in the trash (with the exception of the few P-listed wastes). It is also common to find wrappers, paper towels, exam gloves, and even pop cans in a RCRA waste bin! Make sure your staff understands what the RCRA waste stream is to be used for, and ensure that they are not using it as an open trash can. - Be very careful when donating pharmaceuticals to medical mission groups.
Unless you have spoken to someone in person at the organization, and they have provided proof that the medication can and will be used to benefit others, you should not get involved in this type of donation. Despite your best intentions, it is an unfortunate truth that oftentimes, these sites cannot reuse medications, especially ones that are expired or have been previously opened. Thus, you are simply passing along your medication waste for them to manage, and as RCRA laws state, you MUST maintain cradle-to-grave control of your hazardous waste. If you do not, you are out of compliance and could be fined heavily. - Refuse sample medications from your pharmaceutical reps.
Although it is less common to see sample closets in healthcare these days, no doubt some still exist. The smartest and easiest way to ensure that you aren’t stuck with outdated pharmaceutical waste is to refuse samples. If this isn’t an option for you, check out Dispensary of Hope to see how you can safely and legally donate your short-date samples to patients in need. Additional tips are offered in a MnTAP intern study performed in 2008 to reduce sample waste. - Tell your patients and staff that you care about keeping pharmaceuticals out of landfills.
Take the time to educate your staff and your patients on ways they can properly manage household medication and other household hazardous wastes. Create brochures and posters letting them know why correct disposal is important for environmental and human health, and provide information on county-specific disposal options (such as the Take It to the Box program). Refer to the patient/consumer disposal of pharmaceutical waste section of the Pharmaceutical Waste Topics webpage for more details. - Carefully consider whether or not to purchase chemicals in bulk.
When you end up with outdated facility, cleaning, or laboratory chemicals, many require disposal in the RCRA waste stream. To prevent this waste, you should evaluate the chemical ordering processes used by housekeeping, supply chain, and maintenance staff. “Buy in bulk” discounts offer no advantage if a product expires. If you find that you have more on the shelf than you can use before expiration, try calling others in your healthcare facility network to share your product before it expires, or try listing it on the Minnesota Materials Exchange. - Review opportunities to buy greener products whenever possible.
This is especially true for your housekeeping program. Both Green Seal and EcoLogo have developed stringent criteria in order to authenticate what can be labeled as a green cleaner, and both are well respected certification organizations. Green cleaners may include products such as degreasers, glass cleaners, carpet cleaner, bathroom cleaners, and multi-surface cleaners. Similar strategies can be found under the infection prevention and green cleaning section of this website.
Case Studies, resources, and links
Resource #1: Links cited in the document above (for those who may be using a print version of this information)
- Resource Conservation and Recovery Act (EPA)
- Regulatory Consensus on Health Care Issues (MPCA)
- 10 steps to compliance (MPCA)
- Notification of Regulated Waste Activity (MPCA)
- Search the HWID database
- Information on hazardous waste permitting and Treatment, Storage, and Disposal Facilities (TSDF)
- The Alternate Method to Evaluate Pharmaceutical Waste for the Lethality Characteristic (MPCA)
- DEA’s list of controlled substances
- DEA’s 2012 proposed rule changes for controlled substances
- Occupational Exposure to Antineoplastic Agents (CDC/NIOSH)
- Regulating Antimicrobial Pesticides (EPA)
- Federal Uniform Hazardous Waste (shipping) Manifest
- Hazardous Waste Disposal Companies (maintained by Hennepin County)
Resource #2: Why do we care, environmentally, about proper disposal of RCRA wastes?
- EPA information on PPCPs
- US geological survey (USGS) homepage
- Minnesota impaired waters list
- Washington State Department of Ecology
- Wisconsin Department of Natural Resources and healthcare hazardous waste
- Healthcare Environmental Resource Center (HERC)